8.00 a.m., St. Imier
Teddy Sassier is sitting in front of his computer in the office. Hot coffee in one hand, mouse in the other. It’s a typical start to the day for the wind turbine engineer. “The first thing we always do is check that all 16 turbines are working as they should,” says Teddy. The entire Juvent wind farm on Mont Soleil can be seen on the screen, and every turbine can be clicked to bring up monitoring data for it. “Our job is to quickly identify any anomalies before they cause damage. This can range from overheating motors and incorrect hydraulic pressure to temperature problems with gears.” All normal. Teddy and his colleague Jérôme Lasnier are able to carry out the planned maintenance work on turbine 8: various oil filters in the hydraulic system of the rotor blades need to be changed, as do the back-up batteries for system monitoring. With a car full of equipment, we start our 1,200-metre ascent up Mont Soleil.
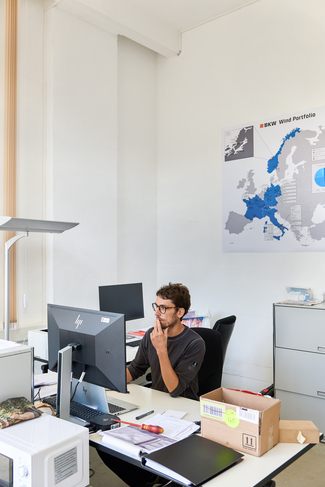
9.20 a.m., Mont-Soleil
We drive to the plot where turbine 8 stands. The farmer’s dog Itti welcomes us as we pass through the electric fence. The turbine grows bigger as we get closer. With its 95-metre-high tower and 55-metre-long rotor blades, it is one of the biggest on the wind farm. Teddy passes me a helmet, a harness and some gloves. After a thorough safety briefing, I join Jérôme in the service lift. It’s not for the claustrophobic – but it’s still better than the alternative: a ladder with 280 rungs.
10.00 a.m., Turbine room
After about seven minutes, the lift reaches the top. We climb a ladder into the small turbine room. For a brief moment, I feel like I’m in a space station. They explain to me what all the different machines do – from the rotor and gears to the generator and transformer. Teddy uses a hydraulic pump to push three large cylinders into the turbine wheel to block the rotor. The two engineers then get to work replacing filters, changing batteries in the control box and carrying out various checks.
10.15 a.m., on top of the turbine
And then the highlight: we reach the roof of the turbine room through a hatch. Secured by two big hooks and ropes attached to our harness, we stand on top of the turbine – my legs feel like jelly. From up here, I can see the Jura Mountains, the Chasseral and the other 15 turbines. A horse down on the ground looks as small as a beetle. When you realise just how massive the three rotor blades are, it’s easy to see how this turbine alone can produce enough electricity for 1,500 households. While I take in the view, Teddy checks various sensors. The data about the weather, wind direction and wind quality is important for positioning the turbine and rotor blades correctly, so that electricity can be produced as efficiently as possible.
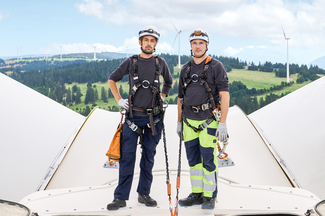
12.05 a.m., lunch break
We are back on the grass at the foot of the turbine. It’s quiet all around us, but for the odd cow bell in the distance. During lunch, Teddy tells me how he ended up landing his dream job: “When I was a kid, I once saw a wind turbine in a magazine. I knew straight away: I want to work on something like that!” Teddy, now 37 and originally from France, set about turning his dream into reality. He kept on training and learning, before joining BKW in October 2021. Teddy checks his phone: no weather warnings. We can go back up again.
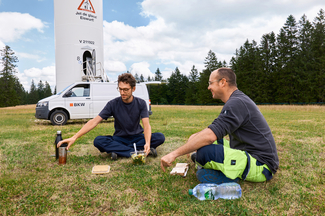
1.20 p.m., in the lift
I’m standing with Jérôme in the narrow lift. We’re chatting about winter on Mont Soleil. Many tourists visit the mountain at that time of year with snowshoes, skis or dogs. If chunks of ice on the rotor blades fall off on a sunny day, it can be very dangerous. That’s why cross-country skiing trails and winter hiking routes don’t lead past the turbines. “We’ve occasionally had to close down the whole wind farm for a few hours on winter weekends because of falling ice. But safety comes first.”
2.30 p.m., in the rotor hub
We crawl on all fours from the turbine room into the rotor itself. Wow – it’s a good thing the rotor blades are still secured! Teddy checks the settings and confirms: “All good.” Even if no one can check them in person, the turbines are still monitored remotely – 24/7, all year round.
“Every season, we carry out routine work and troubleshoot any issues,” Teddy tells me. “This means we have to plan things meticulously, so that the turbines need to be switched off as little as possible. We maintain and monitor all 16 turbines on the wind farm as a two-man team. We take turns working on-call, and the family on a nearby farm also helps us out. Another task is to order the materials on time. “In autumn, we then have to carry out strength tests on all turbines to make sure they’ll be able to withstand the strong winds in winter. Teddy and Jérôme pack up their tools – their work on turbine 8 is complete.
![[Translate to bkw.ch: EN:] Techniker in der Turbine](/fileadmin/_processed_/d/9/csm_13_Ein_Tag_im_Leben_von_BKW_Teddy_Sassier_566_2dc4a13585.jpg)
4 p.m., at the electric fence
The rotor turns in the wind with a steady whirr. We drive away slowly along the gravel road. Itti barks good-bye as we pass the electric fence. What a day it’s been!
Article from Inmotion
This article is from «Inmotion», the magazine for employees of the BKW Group. You can find the entire issue as a PDF here (in German or French).
Comments
BKW is open to respectful online dialogue (our netiquette) and welcomes your comments and questions. For questions that do not fit the topic above, please use the contact form.